Specialist Aluminum Casting Illinois: Accuracy and Performance
Specialist Aluminum Casting Illinois: Accuracy and Performance
Blog Article
Grasping the Craft: Professional Tips for Flawless Light Weight Aluminum Spreading Results
In the world of aluminum expertise, casting and accuracy are critical to achieve remarkable outcomes. Grasping the craft calls for a thorough understanding of the devices and tools at one's disposal, a keen eye for preparing the light weight aluminum alloy to precise specs, and an ingenious hand in employing ideal spreading strategies. Nevertheless, truth mark of a seasoned specialist depend on their ability to achieve faultlessly smooth surface area finishes that raise the high quality of the end product. Quality control and troubleshooting are vital components that can make or break a casting job, guaranteeing that every step is carried out with miraculous care and focus to information.
Important Devices and Devices
Aluminum spreading requires certain tools and equipment to make sure precision and efficiency in the process. Critical devices consist of a crucible, heating system, mold and mildew, and ladle. The crucible, usually made of graphite or ceramic materials, withstands heats needed to thaw light weight aluminum. A well-insulated heater capable of reaching temperature levels over 1200 ° C is necessary to dissolve the metal. The mold and mildew, often made from steel or sand, forms the liquified light weight aluminum right into the desired kind. A ladle is made use of to transfer the fluid metal from the crucible to the mold without spillage.
Additionally, devices like gloves, tongs, and aprons are essential to make certain the safety of drivers dealing with molten aluminum. Tongs supply a protected grip when dealing with warm crucibles and mold and mildews, while heat-resistant gloves and aprons safeguard against unintended burns. Correct air flow systems are additionally essential to remove fumes and make certain a risk-free workplace. Investing in top quality devices and equipment not just improves the accuracy of light weight aluminum spreading but likewise adds to a much more safe and reliable production procedure.
Preparing the Aluminum Alloy
To make sure the success of the light weight aluminum spreading procedure, careful preparation of the alloy is critical. The first action in preparing the aluminum alloy is to thoroughly choose the proper kind of aluminum based on the attributes needed for the last product.
After cleaning, the next critical action is to heat the aluminum to the appropriate temperature level for casting. This procedure, known as alloy melting, makes certain that the aluminum remains in its molten kind and ready for casting (aluminum casting illinois). Additionally, regulating the temperature level during melting is important to avoid overheating or underheating, which can cause issues in the final item. On the whole, precise preparation of the light weight aluminum alloy sets the foundation for an effective spreading process and high-quality outcome.
Optimum Casting Methods
Implementing precise spreading strategies is vital for achieving premium results in light weight aluminum casting processes. The light weight aluminum needs to be heated up to the ideal temperature to reduce flaws like contraction and porosity in the last cast.
Additionally, keeping regular putting speed and pressure is crucial to attaining uniformity in the actors piece. Steady and slow pouring assists protect against turbulence and air entrapment, which can result in blemishes. An additional important facet is the use of degassing agents to remove contaminations and gases from the molten light weight aluminum, resulting in a cleaner last item.
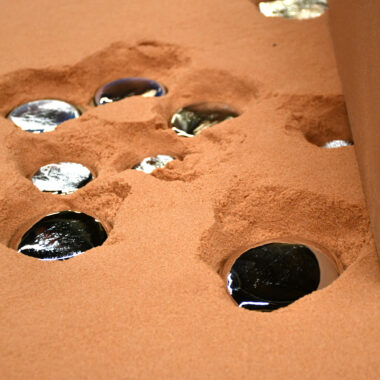
Achieving Smooth Surface Finishes
For suppliers seeking to improve the aesthetic allure and quality of their aluminum spreadings, achieving smooth surface area coatings is a crucial element complying with precise spreading strategies and correct air conditioning treatments. One key method to attain smooth surface area coatings is by making use of high-quality molds that are appropriately prepared and preserved. The mold surface must be diligently cleaned up and covered with release agents to avoid imperfections transferring onto the cast aluminum throughout the cooling process.
Additionally, managing the cooling rate of the aluminum casting is essential for accomplishing a smooth surface area finish. Fast cooling can result in thermal slopes that lead to surface issues, while sluggish air conditioning may create microstructural problems - aluminum casting illinois. By implementing controlled air conditioning procedures, such as utilizing air or water quenching techniques, suppliers can make certain that the light weight aluminum solidifies evenly, lowering the probability of surface blemishes
Along with mold and mildew quality and cooling down procedures, post-casting therapies like shot blasting or chemical etching can further improve the surface area coating of light weight aluminum castings. These techniques assist smooth out any kind of staying roughness or contaminations, causing a remarkable appearance that satisfies the best standards.
Top Quality Control and Troubleshooting
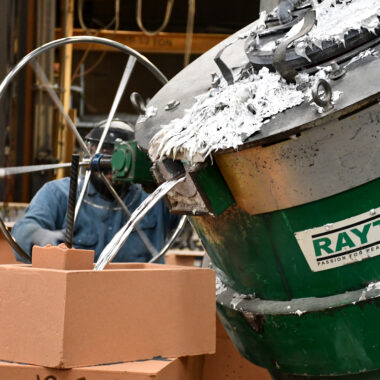
In the realm of troubleshooting, it is vital to have a thorough understanding of usual problems that can happen during aluminum spreading, such as contraction, porosity, or surface area abnormalities. By performing root cause analysis and carrying out rehabilitative steps, makers can prevent these issues from reoccuring in future casting runs. Effective repairing not only boosts the total high quality of cast aluminum products yet likewise boosts process effectiveness and decreases production prices. Continuous renovation with quality assurance and repairing practices is essential to accomplishing perfect cause aluminum casting.
Conclusion
Finally, grasping the craft of light weight aluminum spreading requires essential tools and tools, correct prep work of the light weight aluminum alloy, ideal casting techniques, accomplishing smooth surface area coatings, and carrying out quality assurance steps. By complying with these professional ideas, remarkable outcomes can be accomplished in aluminum spreading processes. Quality assurance and troubleshooting are necessary aspects to take into consideration to make certain constant and high-quality cause light weight aluminum casting jobs.
The first step in preparing the aluminum alloy is to very carefully select the suitable kind of aluminum based on the features needed for the final product.Executing precise spreading methods is vital for accomplishing top notch results in aluminum spreading procedures. By mastering these ideal casting methods, makers can continually generate remarkable light weight aluminum castings.
For suppliers looking for to enhance the aesthetic allure and quality of their aluminum spreadings, attaining smooth surface area coatings additional resources is an important aspect adhering to accurate casting methods and proper cooling procedures.In final thought, understanding the craft of light weight aluminum casting needs important devices and equipment, appropriate preparation of the light weight aluminum alloy, their explanation optimum casting methods, achieving smooth surface coatings, and applying high quality control steps.
Report this page